The Device Chronicle interviewed Max David Falkner, CFO from Abaut, about construction IoT and leveraging cloud and IoT technologies, and Mender OTA software updates, to perform process monitoring and improvement for mining and construction sites.
Remote process monitoring for managers in construction IoT
Imagine this scenario: where a construction site manager or mine manager can sit in an office remotely and a large construction site remotely, in a way that is much better than if they were onsite, and just like an industrial plant. This is the promise and fast becoming reality of IoT and AI in construction and mining. Line construction sites such as rail and streets are especially hard to monitor. Max David Falkner, CFO at Abaut explains “The telematic data is insufficient to provide the right insights, it is machine focussed for maintenance but not for the process that the machine is involved in. If the machine is not working, why is it not working? In line construction sites, it is very hard to capture surround information, there is inbound material, there is an excavator in a machine, is he moving material or is he placing material that is coming in. Without edge devices and cameras on the machine which can survey the processes and productivity, then it is next to impossible to monitor what is happening in a line construction site.”
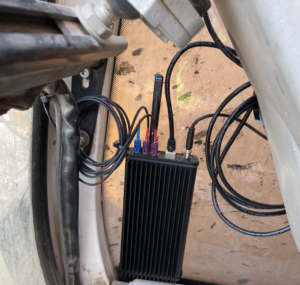
Edge data generator and processing services provider Abaut is solving the challenge of project process tracking in civil engineering mining and construction sites. Max David further explains that monitoring civil engineering mining and construction sites can be very challenging. The objective, which can be challenging to achieve with high precision, is to record and measure process efficiency and progress. The problem is exacerbated by the fact that large construction sites are often fragmented consisting of many smaller construction sites on a single larger site.
The business needs to document processes as accurately as possible to assist with proofing for invoices and dispute resolution. In the absence of the use of AI and IoT, the documentation of activity on construction sites comes with huge administrative burden and costs. Telematic information as a source is insufficient as it supplies one dimensional data such as location of the machine and whether it is on or off. It doesn’t supply detailed information on whether the process is progressing as it should be. Furthermore, drones have limitations and cannot identify and report on machine intensive processes.
From opaque processes to deep understanding in construction IoT
The application of AI and IoT technologies also combats opaque processes where there is lack of transparency on what is really happening in the process. Increased transparency leads to greater efficiency and productivity while the technology allows for employees’ privacy to be protected and respected. While if the processes are not monitored and reported upon properly, there is every chance of cost overruns and delays in the delivery of the project.
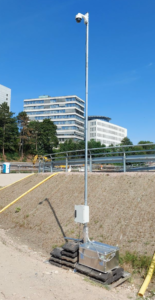
Machines become intelligent process trackers in construction IoT
Construction machines can now be used as a medium to capture the reality of the project on the sites by having embedded devices installed on them. These edge devices are plug and play and do not rely on the CANbus of the machine to conduct the monitoring and analysis. These devices also have the advantage of working on a mix of machines across the construction fleet. Once fitted to the construction machines, Abaut’s edge device technology captures inertial measurements for data generation such as vibration, GDPR-compliant images, and delivers a dynamically trained machine algorithm from the cloud to the edge device via over the air software updates provided by Mender.io. This edge device can work with 360 degree cameras (the Abaut S view) that are attached to the machines, and mobile cameras (the Abaut M view) and even laser-based Lidar systems for object and person detection in close proximity to the machines. The edge devices connect via Wi-Fi, bluetooth, machine to machine protocol over 5G and LTE 4 and narrowband IoT.
A cloud infrastructure captures data such as localisation, inertial measurements, time stamps, images, design and schedule, and transforms the information into insights that can be used to improve decision making. The cloud infrastructure which Abaut call “Core” can be used to continually monitor processes and progress, and to capture, map and process site images automatically without the need for human intervention or interference with site operations. With the rich insights that can be obtained through cloud analysis, process bottlenecks can be identified and corrected.
Max David explains another benefit of working with Abaut: “The company is OEM-independent and delivers dashboards that are easy to understand which is important for mining and construction professionals. Several of Abaut’s employees have construction and mining backgrounds. Max David also outlines another benefit of partnering with the company: “Large machine suppliers such as Komatsu and Cat have monitoring solutions which can be used in both their own and 3rd party machines, but then the risk can be vendor lock-in and machine upselling. So by using an independent service provider for edge data generation and processing, construction and mining companies may be able to decrease machine size by really understanding progress and machine performance. Medium sized companies need help to save on costs.”
Use cases in process monitoring
There are several use cases for optimising a vehicle fleet on-site, and for optimising productivity.
There may be 10 construction sites in parallel with one excavator, then the case is to use the edge device and cameras to automate the monitoring. Medium-sized construction companies may have 15 of these excavators that would need to be monitored.
In special foundation engineering, floors must be built that are more robust in streets and motorways. Max-David explains “A concrete box must be constructed so you need a large drill rig and this is monitored with cameras. Machine vision is needed to classify images, and these images are then processed in the cloud after they have been detected by the motion data of the sensors on the edge.”
Management and business analysts can also use the data insights from the edge devices to assess productivity curves to see if steepness is retained, to see if productivity increased or decreased within a certain timeframe, and to look into the data to find the bottlenecks so the site can be optimised by doing a longitudinal analysis.
Another use case is maintaining live views of machines as they work. “Machines could be in the wrong locations or doing wrong activities and now rather than driving around the site, the manager can remotely manage the productivity of the drivers and material costs such as fuel used in the vehicle.”
OMYA mines industrial minerals used in paper and plastics manufacturing. Abaut sensors and cameras are used across 150 mine sites so that a network of regional managers can monitor productivity and detect bottlenecks at the sites. While at Deutsche Bahn, managers can analyse logistics and sub contractor performance. Sub contractors shifting gravel by the truckloads, and managers can see precisely how many trucks came and were they filled or not filled, important for Deutsche Bahn, from which routes how many trucks are coming in. This helps Deutsche Bahn to manage costs and performance and prediction of resources required. These data insights allow Deutsche Bahn managers to understand how many trucks are required to get the job done, with an analysis of day by day truck loads delivered.
Importance of OTA software updates
Torsten explains that Abaut’s embedded devices are based on a Toradex i.MX 7 module, a modem wi-fi with an MCU for controlling and IMU for motion sensing. There is an SD card for storing and a sim card for data transmission. The device runs on a battery, there is no external power supply. A Yocto Zeus image is used for the operating system, and Mender will be used for OTA updates. A MCU is used for power control and an A/B partition is used for updating the MCU. “Mender was particularly impressive for OS updates and you just can’t break it!”
We wish Max David, Torsten and their colleagues at Abaut well on their journey to enabling insights from data captured through machines on mining and construction sites.