The Device Chronicle interviews Roger Feist, Director of Digital Solutions, Achenbach. Roger describes the smart factory enabled with IoT device management. This includes edge devices with OTA software updates for Yocto, and Google IoT. Get the full story on this impressive project from this machine maker in our Smart Manufacturing Strategy Ebook.
Industrial manufacturers such as Achenbach Buschhütten GmbH & Co. KG are embracing the smart factory based on IoT device management and edge devices with Mender providing the robust and secure OTA software updates to the Yocto build of the OS and firmware of the IoT gateway devices on the production level controllers. Mender partner Sotec provided the overall solution.
There are great industrial companies that teach us to always be innovating – now it’s based on digital – and we need to learn from these. They embrace digital to make it work for their businesses. These types of companies aren’t afraid to embrace digital because of its complexities, but rather exploit it for its endless great possibilities. These possibilities are realised by becoming a smart factory through great IoT device management alongside leveraging the likes of Sotec Cloudplug edge devices, Siemens PLCs, Google IoT, Cloud and Machine Learning technologies.
Digital transformation
Firstly, executives in these types of brave manufacturing companies will never ask the question: “What is this connectivity thing and why is this happening on my shift?” This question came up in a conversation with an IOT executive in an appliances company on the struggles he faced trying to overcome the resistance to digitalisation in a more traditional product engineering company. But let’s issue a note of caution to more complacent companies. They should embrace digital as the “bytes are overtaking the atoms”. If companies aren’t proactive in reimagining product and process design by putting software, data, cloud and embedded intelligence at the centre in the physical shell, then it could be too late.
IoT device management partners
Some traditional companies who have stood the test of time are providing shining examples of how digitalisation can be done successfully. More often than not, they make the smart realisation quickly that they cannot do it themselves in-house and that they need software expertise to complement their own operational excellence. This is a marriage made in heaven and one that has been rightly identified by McKinsey as a great strategy pursued by the leader organisations.
Machine maker in need of IoT device management
We were introduced by our technology partner and Google Cloud IoT Core partner Sotec to what they humorously described as a “540 year old start-up” such is the company’s zeal for continued innovation. German machine manufacturer Achenbach Buschhütten GmbH & Co. KG has been processing metals, and rolling aluminium since 1452. It has always looked to harness advances in technology to move its business forward. In the middle ages, the low quality of the iron ore found in their vicinity forced them to develop an innovative hammering method to get it to a quality grade that would make it useful for the local craftsmen. The discovery of better ore in the Ruhr in the industrial revolution forced the company to shift focus again to becoming a foundry and then to become aluminium rolling machine makers.
PLCs and IoT device management in the smart factory
Globalisation and the increasing movement of their business from Europe to Asia forced them into a rethink on how best to support their customers. Especially when a new machine was commissioned in a plant and afterwards when the operators were looking after the machine themselves. Its Director of Digital Solutions Roger Feist describes it as a potential “black hole”: A time when the company is not sure how a customer is getting on with a new machine. Could there be dissatisfaction, or serious issues that are not being communicated?” Digital technology helps to recognise these issues so that the provider can address them, or even use a predictive path to anticipate issues and solve them before the customer realises there’s an issue.
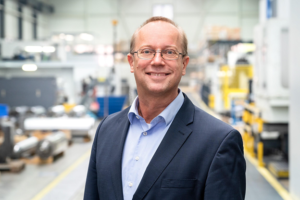
A new IoT device management and Google IoT platform
Achenbach has invested heavily in what is described as a manufacturing automation reference architecture. This means that the company has a cloud platform that integrates data collected by IoT sensors from the production machines, and is controlled and transmitted by a system of gateways and controllers, to the cloud for analysis with machine learning and big data techniques.
Edge devices in the smart factory
The impact of this technology investment has been a significant rise in productivity and customer satisfaction, and the company is able to move from a paradigm of a single qualified data stream from machines via edge devices that only address a single use case to a data first approach. This is where the data is collected, processed and then analysed to serve multiple use cases, some known and other unknown beforehand. Isn’t this what every company wants to be able to do? To be able to extract insights from their operational data to solve business problems.
Use cases for edge devices and Google IoT
The kind of use cases that can be solved with this data first approach are manifold and include the following in the case of a production machine manufacturer.
- Automation to eliminate anomalies in production
- Performance comparisons between one time period and another
- Breakdown prediction with analysis of machine drift and parts deterioration
- More accurate product quality reports for the customer
Yocto support in the smart factory
To get to this point takes bravery from company leadership just to dive in and learn what IoT, data, cloud and machine learning can do for their business processes. They must also appoint and empower “natively digital” executives who also understand operations and the shop floor culture, and to make brave technology selections. In the case of Achenbach it is Roger who partners with Sotec for the IoT gateways, and its Scitis.io platform based on Google IoT Core for the ML and big data analysis. Mender provides the robust and secure OTA software updates to Yocto, the OS, applications and firmware of the IoT gateway devices. And there are two additional lessons here. In manufacturing, data science doesn’t work in a lab. The data must be collected, processed and analysed in almost real time – to the magnitude of 100s of milliseconds. In this way it can properly support operational decision making.
OTA software updating and the smart factory
To keep the data flowing in almost real time, the IoT gateways must be kept operational. If the IoT gateway loses power it needs to be able to recover quickly and avoid failure from updating. It’s not easy to find a specialist technician to fix a “bricked” device in a manufacturing plant on the other side of the world. HQ must maintain remote contact to the devices. This is where update roll backs are crucial and then of course..
Only authorised people can deploy authorised software to authorised devices.
Which leads to
Only the right people deploying the right software to the right devices
Read about the Triangle of Trust.