The Device Chronicle shares some highlights from the Open Industry 4.0 Alliance Demonstrator Day with a focus on Industry 4.0 technologies.
To kick off proceedings, Ricardo Dunkel, Technical Director, at the Alliance provided an overview of the OI4 Reference Architecture and the Asset Administration Shell (AAS). Ricardo explains that the overall goal is to connect the OT world to the IT world so as to realise the benefits of the digital twin.
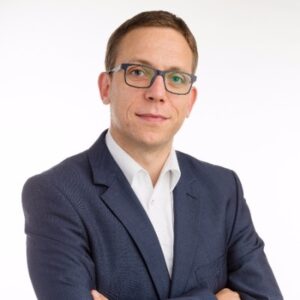
There are 4 essential layers in the OI4 reference architecture. On the shop floor or “OT” arena, there are the open edge connectivity and open edge computing layers. There is also a zero layer which consists of the physical things on the shop floor including machines, compressors, PLCs, vehicles, gateways, sensors and actuators.
In the cloud layer, you will find the open operator cloud platform which is a home for an Alliance member to provide services to customers for their devices and machinery in the production layer. There is also the common cloud central. The cloud in this context can also mean an on-premise system or an Azure or AWS hosted system. Cloud is simply a catch all term to say that you need northbound applications to run the digital twin.
There are vertical perspectives across the architecture: With so many companies involved in the Alliance, there is a need to create a common understanding.
Security covers all the layers and must protect against cyber attacks and provide proper data governance.
An OI4 marketplace or “app store” allow the OI4 members to provide some service products with specialisms on different levels from cloud to edge applications, and on devices. These applications should be plug and play.
Edge layer
There are different protocols in a brownfield environment so protocol adapters and server bricks are needed to interact and communicate with equipment on the shop floor. Open edge computing such as a message bus. There is a working group to support this.
Open operator cloud
This includes platform services such as monitoring and logging. Ricardo explains that the AAS infrastructure is also provided here and this is the heart of the digital twin. Every functionality in the device twin needs to be communicated centrally through the AAS infrastructure.
Common cloud central
This is a collaboration layer with a concentration on the AAS components. The AAS reference registry can connect server cloud platforms of open cloud operators.
Ricardo explains that the reference architecture doesn’t need to be implemented in its entirety by all members. In fact, members can select the components that make sense to their customer’s needs. Domain specialists are needed to help the technical workgroups and the industry use case workgroups.
Ricardo showcased the OI4 Demonstrator Setup RI 1.0 with the open operator cloud platform in the “cloud” and open edge computing in the “shop floor”. The AAS server and registry are included, as are a service layer for onboarding and health checking; an OEC connector for edge connectivity, and then a message bus and Runtime and Docker Framework for software in the Open Edge Computing layer. The communication starts with the message bus which retrieves information from the OEC registry and the OOC Connector communicates to the cloud platform. This is the case for both the onboarding and the health data exchange. The OI4 service layer communicates with the AAS infrastructure and after onboarding, health data can easily be exchanged.
Demonstrator on multi vendor asset onboarding & condition monitoring
Michael Riester, Senior IoT Architect for Industrial IoT at Endress + Hauser, presented a demonstrator. This demonstrator focussed on multi vendor asset onboarding and condition monitoring, and multi vendor interoperability.
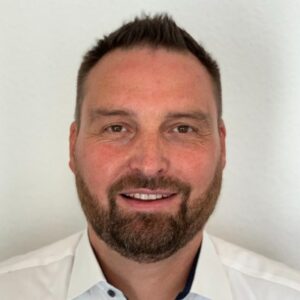
Michael is the lead for the open operator cloud workgroup. He started by outlining the challenges faced by plant operators. They have to inherit and manage multi-vendor and legacy asset environments. They have different levels of maturity of digitalisation. They must convince management of benefits of digitalisation, and are also afraid of growing complexity. They also face barriers in implementation of silos, high complexity and often business approaches.
The demonstrator used the Open Edge Computing Platform, the OI4 Reference Implementation for the AAS infrastructure; and the concepts of the Asset Administration Shell. This is the foundation as the asset has to be onboarded and its health checked to be the basis for other use cases.
The benefits for the operators from the demonstrator include:
Better Asset Master Data Management:
- More transparency for shop floor activities
- Improves asset performance
- Improves product quality
- Increases process productivity
Automatic onboarding of assets
- Reduces systematic errors
- Reduces manual data management
- Increases access speed and ease of asset onboarding
- Improves the quality of master data in other processes
Demonstrator on health states of cooperative robots
A second demonstrator was presented by Konrad Heidrich on a cooperative robot integrated with the OI4 Reference Architecture via AAS. Konrad is Senior IoT Solution Architect at Hilscher and Group Leader of the OI4 open edge computing group. He stressed that a common standard is needed for the digital twin so that collaboration is possible for different vendors across different sectors. In the demonstrator cooperative robots are coupled to their physical counterparts via digital instances and digital twins and provide their health states. Namur NE 107 Health States are available and this allows for programmatic evaluation and linkages to higher level manufacturing process states. Ultimately, this helps to optimize the production process. Konrad concludes that the provision of OEE and telemetry data for the robots via the Asset Administration Shell of the OI4 will be the next step in the project.
Other demonstrators from ifm, M&M Software and Dunkermotoren were also featured in the Demonstrator Day.
Interesting industry use cases
A process industry use case which was multi vendor and multi protocol was also presented. This project won an OI4 Implementation Award. In this use case, valuable data about machines was liberated and sent northbound from the edge to the cloud. Daan Wortel, MD, Duurzaamheidsfabriek from the Flow Center of Excellence, explained that the project goal was to provide a generic means to onboard devices and sensors and provide northbound data communication; and if there are advantages to using the OI4 approach and publications. The project is a strategically important field lab in Dordrecht close to a large maritime, logistics and chemicals industry hub in Rotterdam.
Jules Oudmans, Consulting Director, UReason, and Thomas Neumann, Business Development Manager, M&M Software, explained how the project involves getting data from pressure transmitters, flow transmitters, control valves, motors and pumps. The OI4 guidelines are applied to unlock the data in 4 20Ma + HART, HART IP, IO-Link, and from hardware provided by OI4 members including Wago, Balluff and Endress+Hauser. From field to edge to cloud, an assessment is being done to understand what it takes to process and reuse this data.
A second industry use case came from the Food & Beverage sector. Simon Stark, Business Development Manager, Multivac, outlined the advantages of having members such as Bizerba, Emerson Aventics, Sick, Busch, Schiwa, Handtmann and Weber involved in a workgroup focussed on Food & Beverage.

The two practical use cases in the group are a) a line analyser project between Multivac and Schiwa, and b) an analysis of sensoric and component integration for energy use and production optimisation. As sector experts, providers and competitors, they were able to work through the OI4 workgroup to understand the use cases and improve outcomes. Multivac and Schiwa are competitors, one providing packaging machines and the other providing meat slicing machines. The Schiwa high performance meat slicer has been integrated into Multivac’s smart services to create new value for the customer. All the OEE data from the Schiwa slicer can be accessed by the customer and Schiwa can use Multivac’s infrastructure to provide new smart services.
All the presentations from the Connect to Open Implementation Demonstration Day are available here.
Northern.tech and Mender.io – the provider of the Device Chronicle blog is a member of the Open Industry 4.0 Alliance.