The Device Chronicle interviews Coskun Islam, Head of Industrial IoT at Sandvik Manufacturing Solutions – DPA Dvision, shares some perspectives on industrial IoT and digitalisation on the shop floor.
Sandvik provides the cutting tools for machining and the CAM software to plan the machining process of how CNCs and the robots move to cut the shape. Coskun is in the R&D division of Sandvik, and his group uses small industrial PCs to deploy software that collects data from production machines, and uses internal networks to deploy development.
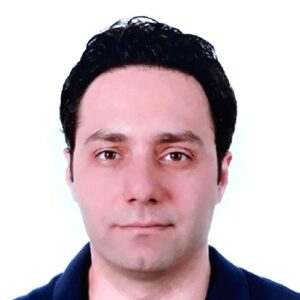
Coskun’s group develops and tests next generation digital technologies by deploying them to their customers who are partners or “lighthouse” factories. These are customers who help co-develop new innovations, and act as testbeds for assessing the effectiveness of new technologies. Coskun says “The partners see the power of digitalization and get their hands on multiple integrated solutions for a more automated manufacturing flow with increased efficiency.”
On-premise preferred for shop floor data analysis in industrial IoT
Coskun further explains that there is a big change happening: “moving from mechanical machines to cyber physical infrastructure and industrial IoT, and customers have valid security concerns around transferring data to the cloud.”
Data processing and analysis on the shop floor, this is all done on the local network normally. A service system consumes the information within the factory for local analysis. Some of the customers have a preference for on-premise set ups for processing and analysis of their shop floor data. “The ball can only be thrown so high, the customers need to be convinced of the benefits of change as every process is working well but can be tuned further with new digital technologies. We must balance different expectations and different ways of working, and not so much automation, but suggestions for improvement so gradually customers embrace the value.”
There are also cloud solutions to consume data at the process planning stage: which covers how to utilize a cutting tool for the machining process requires information from the cloud. Coskun says “Shop Floor data is not sent to the cloud (even though we are ready for it architecture-wise). Data processing mostly happens on the edge PCs and the insights from the data can be transported to the cloud.”
Coskun continues to say that Sandvik has embraced digitalisation and that it is being taken seriously in a broader spectrum in the last few years. Sandvik as a provider of cutting tools for machining has applied digital in basic manufacturing processes, but it is also looking more broadly at the overall manufacturing shop floor experience and the overall product lifecycle. The company is now really stepping into the software space with acquisition in process planning and quality assessment software, and looking into digital expansion in its activity areas and bringing new products to their customers.
Sandvik started in cutting tools machining but expanding to provide digital solutions. Coskun explains that the company wants to make things smarter, remove the pain points for customers, and make the software solutions in manufacturing processes smarter based on knowledge accumulated within the company.” He asks “Can we make smart suggestions to the customers for more efficient and faster manufacturing process planning and execution?” He explains that the company also wants to make things easier and smoother for less experienced customers, while making optimization tools available for the customers who are power users on the leading edge of digital adoption – using data from the machines and the product’s journey to perform better manufacturing system planning.
Weaknesses in the feedback loop
Coskun explains a common problem on the traditional shop floor: “You plan things, the machine has a computer to get the job done, but the feedback loop from the shopfloor to the manufacturing process planning has traditionally been weak. The human is generally the feedback provider.” Coskun and his colleagues want to create feedback loops for machine data and metrology data, and use that data from the manufacturing process and then also do indirect quality assessment of the processes. This will increase traceability, and offers business benefits such as greater control, production efficiency, and the ability to increase sustainability.
OTA software updates and Industrial IoT
Coskun sees the strategic benefits of OTA software updates in industrial IoT for cost reduction and optimisation. “Machine monitoring devices must still be manually updated by the engineers, so there would be savings and efficiency benefits from OTA software updates for both the machine builders and the customers. The cost is especially high for CNC machines.” Digitalisation will become the facto on the shop floor but it will take some years yet Coskun concludes.
We wish Coskun and his colleagues at Sanvik well on the digitalization and industrial IoT journey.